The Importance of Cleaning and Maintenance in Double-Layer Stainless Steel Reactors
Double-layer stainless steel reactors play a pivotal role in chemical processing industries due to their robustness, versatility, and excellent heat exchange properties. To ensure their continued efficiency and performance, regular cleaning and maintenance are essential. Proper care helps to extend the reactor’s lifespan, optimize chemical reactions, and prevent contamination or corrosion. In this article, we will explore the most effective methods for cleaning and maintaining a double-layer stainless steel reactor, ensuring the reactor remains in optimal condition for a prolonged period.
The importance of maintaining your equipment cannot be overstated. Without proper cleaning, chemical residues can build up, affecting reaction outcomes, cross-contaminating products, and potentially damaging the reactor. By understanding the maintenance procedures specific to double-layer reactors, industries can reduce downtime, improve product quality, and maximize operational efficiency.
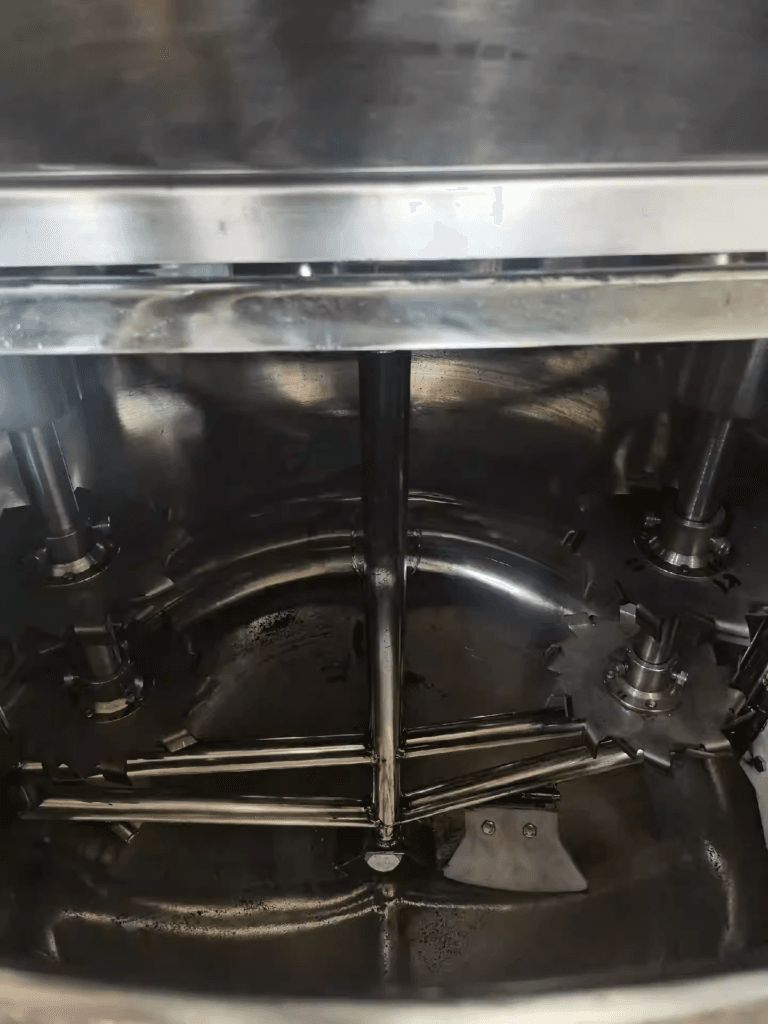
What Is a Double-Layer Stainless Steel Reactor?
A double-layer stainless steel reactor consists of two layers of stainless steel. The inner layer holds the material undergoing reaction, while the outer layer is typically filled with a heating or cooling medium. This dual-layer design facilitates excellent temperature control, ensuring the internal contents are heated or cooled evenly and efficiently. Double-layer stainless steel reactors are used across industries, from pharmaceuticals to food processing, where precise temperature regulation is critical for successful outcomes.
Why Is Cleaning and Maintenance Important?
Cleaning and maintenance are integral to the proper functioning of any double-layer stainless steel reactor. Regular maintenance prevents damage to the reactor’s inner and outer layers, keeps the reaction environment contaminant-free, and ensures optimal heat transfer. Moreover, a well-maintained reactor operates efficiently, reducing the likelihood of breakdowns or costly repairs.
There are several reasons why cleaning and maintenance should not be overlooked:
- Prevent Contamination: Residual chemicals can affect the purity of future reactions, leading to cross-contamination or compromised product quality.
- Extend Equipment Life: Regular maintenance minimizes wear and tear, ensuring that the reactor remains in excellent working condition for many years.
- Improve Reaction Efficiency: A clean reactor ensures proper heat transfer and prevents irregularities that can affect reaction rates.
- Reduce Downtime: Proactive cleaning and maintenance prevent unplanned stoppages, allowing for uninterrupted production.
Best Practices for Cleaning and Maintaining a Double-Layer Stainless Steel Reactor
To ensure the double-layer stainless steel reactor operates at its full potential, several steps should be followed for cleaning and maintenance. These procedures help to ensure that the reactor is free of residues and operates safely and efficiently.
1. Cleaning After Each Use
Proper cleaning begins after each use of the reactor. It is essential to remove any leftover chemicals, residues, or reactants that could interfere with future reactions. The cleaning process involves:
- Flushing: After use, rinse the reactor thoroughly with water or a suitable solvent to remove any loose residues.
- Chemical Cleaning: For stubborn residues, use an appropriate cleaning agent. Ensure that the cleaning solution is compatible with both the reactor’s material and the chemicals previously processed.
- Drying: After cleaning, it is important to dry the reactor thoroughly to avoid any moisture buildup that could cause corrosion or affect future reactions.
2. Routine Inspection for Wear and Tear
Routine inspection is critical in cleaning and maintaining a double-layer stainless steel reactor. Inspect both the inner and outer layers for any signs of wear, corrosion, or physical damage. Look for cracks, dents, or signs of contamination that could affect the reactor’s performance.
- Check the Gaskets and Seals: Ensure that the gaskets and seals are intact to prevent leakage during operation. Replace any worn or damaged seals promptly to maintain the reactor’s integrity.
- Examine Heating and Cooling Systems: Regularly check the heating or cooling systems, including pipes and jackets, for any clogs, leaks, or damage.
3. Descaling and Decontamination
Over time, mineral deposits or chemical residues may build up, especially if the reactor is used for high-temperature reactions or contains substances that tend to form deposits. Regular descaling helps to remove these residues, preventing blockages and ensuring efficient heat transfer.
- Use Appropriate Descaling Agents: Choose descaling agents that are compatible with stainless steel and the substances processed. Be cautious of the concentration to avoid damage to the reactor surface.
- Rinse Thoroughly: After using a descaling agent, make sure to rinse the reactor thoroughly to remove any leftover cleaning agents.
4. Lubrication of Moving Parts
For reactors with moving parts, such as mixers or stirrers, lubrication is essential to ensure smooth operation. Regularly apply the appropriate lubricant to prevent friction and wear, which can cause parts to break down prematurely.
5. Check for Leaks
Regularly inspect for leaks in the system, especially around gaskets, seals, and joints. A leak in the system can lead to operational inefficiencies, contamination, or even dangerous chemical reactions. If any leaks are found, repair them immediately.
Proper Storage and Handling of Double-Layer Stainless Steel Reactors
After cleaning, proper storage and handling of the reactor are essential for its longevity. Ensure that the reactor is stored in a clean, dry environment, and avoid exposing it to harsh chemicals or extreme temperatures during idle periods. Additionally, ensure that all connections, seals, and valves are closed tightly to prevent contamination.
Tips for Preventing Long-Term Issues
- Avoid Overheating: High temperatures can cause expansion and contraction of the stainless steel, leading to potential damage. Monitor the reactor’s temperature carefully to prevent overheating.
- Use Compatible Chemicals: Ensure that the materials and chemicals used in the reactor are compatible with stainless steel to prevent corrosion or damage.
- Perform Regular Maintenance Checks: Schedule routine checks to assess the condition of your reactor. This helps identify issues early before they develop into major problems.
Why Choose EquilRxnLab for Your Reactor Needs?
If you are looking for high-quality double-layer stainless steel reactors, EquilRxnLab offers a range of durable and reliable options. For more information on our reactor products, visit our website: EquilRxnLab Stainless Steel Reactors.
Stay connected with us on Instagram for updates on our latest products and maintenance tips.