Introduction to Corrosion-Resistant Reactor Design
In the field of chemical engineering, reactor design is crucial for ensuring the efficiency, safety, and longevity of industrial processes. One of the most important factors influencing reactor performance is its resistance to corrosion, particularly in environments where aggressive chemicals and extreme conditions are common. Corrosion-resistant reactor design is an essential aspect of creating reactors that can withstand harsh environments, ensuring that operations run smoothly without the need for frequent maintenance or replacements.
The need for corrosion resistance in reactors arises from the high cost of equipment failure, downtime, and product contamination. Whether it’s a lab-scale experiment or large-scale industrial production, having a reliable, corrosion-resistant reactor is essential. This article explores the key features of corrosion-resistant reactor design, the materials used, and the advantages they bring to various applications.
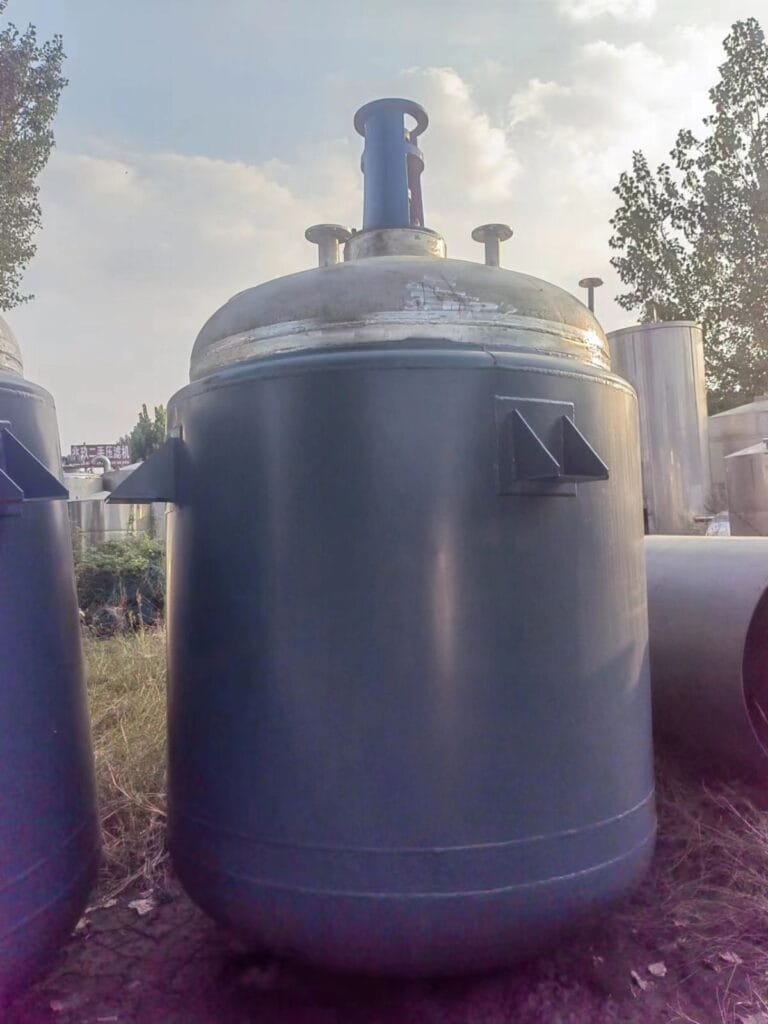
Key Features of Corrosion-Resistant Reactor Design
Material Selection
The foundation of any corrosion-resistant reactor design lies in the choice of materials. Stainless steel is a common material used for constructing reactors due to its excellent resistance to rust, chemical corrosion, and high temperatures. For industrial-scale applications, choosing the right grade of stainless steel is vital. For instance, reactors like the EquilRxnLab Stainless Steel Reactor utilize high-quality stainless steel alloys that are designed to endure aggressive chemical reactions without degradation.
The alloy composition of stainless steel, particularly the presence of chromium, nickel, and molybdenum, contributes significantly to its corrosion resistance. These materials form a passive layer on the surface of the metal, preventing corrosion even in highly acidic or basic environments. Additionally, corrosion-resistant coatings or linings can further enhance the reactor’s longevity by adding an extra layer of protection against chemical attacks.
Pressure and Temperature Tolerance
Corrosion-resistant reactor designs are also engineered to handle high-pressure and high-temperature conditions, which are common in many industrial chemical processes. The ability of a reactor to resist corrosion under such extreme conditions ensures that the reaction continues efficiently without compromising the integrity of the system. For example, reactors used in chemical synthesis, pharmaceutical production, or petrochemical industries often require designs that can handle pressures exceeding 100 bar or temperatures above 300°C.
By integrating corrosion-resistant materials with advanced pressure and temperature control systems, modern reactors are capable of maintaining optimal performance throughout the reaction process. This, in turn, reduces the likelihood of system failures and improves overall productivity.
Leak Prevention and Sealing Mechanisms
Leak prevention is another key consideration in corrosion-resistant reactor design. Even the slightest leakage of volatile or hazardous materials can result in significant safety risks, environmental contamination, and financial loss. Reactors that incorporate specialized sealing mechanisms, such as PTFE gaskets, O-rings, and pressure relief valves, ensure that the system remains airtight and safe during operation. These sealing materials are selected for their chemical resistance properties and ability to withstand extreme temperatures without degrading.
Moreover, corrosion-resistant designs help prevent leaks in critical components such as joints, flanges, and valves, which are common points of failure in non-corrosion-resistant reactors. Ensuring leak-free performance not only improves safety but also boosts the efficiency and reliability of the reactor.
Advantages of Corrosion-Resistant Reactors
Increased Longevity and Reduced Maintenance
One of the primary benefits of using a corrosion-resistant reactor is its extended lifespan. Unlike reactors made from standard materials, corrosion-resistant reactors are less prone to wear and tear caused by chemical exposure, rust, or scaling. This results in fewer breakdowns and a significant reduction in the need for maintenance and replacements.
For businesses, this translates into cost savings, as they can avoid the frequent repair or replacement costs associated with traditional reactors. The durability of corrosion-resistant reactors ensures that they continue to perform effectively for years, even under demanding conditions.
Enhanced Process Safety
Corrosion-resistant reactor design also contributes to enhanced process safety. Corrosion can weaken reactor walls, leading to cracks, leaks, or even catastrophic failure in some cases. With corrosion-resistant materials and design techniques, the risk of failure due to material degradation is minimized. This not only protects workers from potential accidents but also safeguards valuable chemical processes from disruption.
By utilizing corrosion-resistant reactors, industries can ensure that their processes are safer, more predictable, and less likely to result in hazardous situations. This is particularly critical in sectors such as pharmaceuticals and food processing, where safety and compliance with regulatory standards are paramount.
Higher Efficiency and Consistency
Corrosion-resistant reactors are designed to maintain consistent performance over time, ensuring that chemical reactions proceed without interruptions or inefficiencies caused by material degradation. This level of reliability is especially important in processes where precision is crucial, such as in the production of specialty chemicals, fine chemicals, and pharmaceuticals.
Additionally, corrosion-resistant reactors are more efficient in terms of energy use. As the materials do not degrade over time, the reactors can maintain optimal thermal conductivity, allowing for better heat management during reactions. This efficiency not only improves reaction yields but also reduces the energy costs associated with heating and cooling the system.
Applications of Corrosion-Resistant Reactors
Corrosion-resistant reactor designs are utilized across a wide range of industries and applications. From the chemical industry to pharmaceuticals and food production, these reactors are essential for any process that involves aggressive chemicals, high temperatures, or high pressures.
- Chemical Synthesis: Corrosion-resistant reactors are used extensively in the production of chemicals where strong acids, bases, or solvents are involved. These materials would otherwise cause corrosion in standard reactors.
- Pharmaceutical Manufacturing: In pharmaceutical production, corrosion-resistant reactors are essential for maintaining sterile conditions and ensuring the purity of drugs. The reactors must withstand aggressive solvents and high temperatures without contaminating the product.
- Petrochemical Processing: The petrochemical industry relies heavily on corrosion-resistant reactors for refining and processing crude oil. These reactors must be able to handle corrosive chemicals such as sulfur compounds, which are present in oil.
- Food and Beverage Processing: In food production, corrosion-resistant reactors help ensure that chemical reactions proceed without contamination. This is especially critical when dealing with food-grade chemicals or ingredients.
Innovation in Corrosion-Resistant Reactor Technology
Companies like EquilRxnLab are at the forefront of innovation in corrosion-resistant reactor technology. By offering high-quality stainless steel reactors, such as the 200L Stainless Steel Reactor, they provide advanced solutions that meet the needs of industries requiring durable and reliable equipment.
These reactors are designed with user-friendly features, such as precise temperature and pressure controls, to ensure smooth operation. By leveraging advanced materials and engineering techniques, EquilRxnLab ensures that their reactors can withstand the harshest conditions, providing businesses with long-lasting, high-performance equipment.
Further Reading and Resources
For more information about corrosion-resistant reactor designs and to explore EquilRxnLab’s product offerings, visit their official product catalog. You can also follow their updates on YouTube, Instagram, and Facebook for the latest innovations in reactor technology.
By investing in a high-quality corrosion-resistant reactor, industries can ensure the longevity, safety, and efficiency of their operations, ultimately driving success in their respective fields.