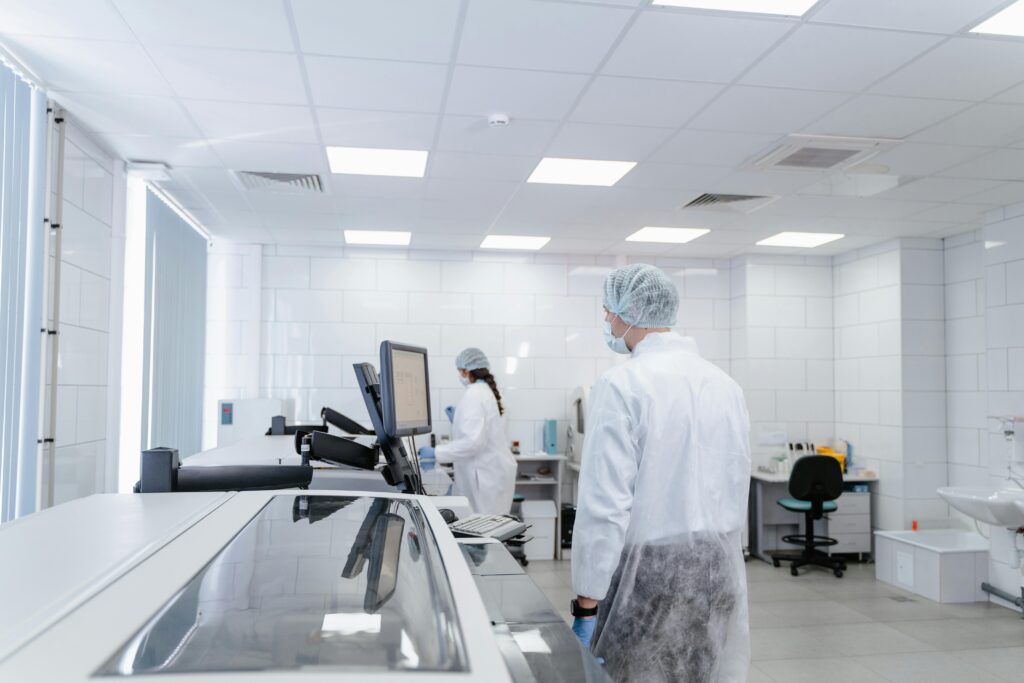
1. Introduction: The Importance of Reaction Design
In chemical research, reaction design is a critical factor that determines the success of an experiment. By optimizing reaction conditions, researchers can increase yield, improve product purity, and reduce the formation of by-products, thus enhancing overall efficiency. Reaction design involves several factors, including reaction time, temperature, pressure, and solvent choice, all of which directly affect the progress and outcome of chemical reactions.
2. The Role of Equipment in Reaction Optimization
Laboratory instruments play a crucial role in reaction design. Advanced equipment allows researchers to precisely control and optimize experimental conditions. Below are some commonly used devices in reaction design and their applications:
- Stainless Steel Reactors: Ideal for high-temperature and high-pressure reactions, they maintain stable reaction conditions and are commonly used in organic synthesis.
- Single/Double Glass Reactors: Their transparency allows researchers to observe the reaction process in real-time. Double-layer designs allow the circulation of heating or cooling media, providing precise temperature control for sensitive reactions.
- Low-Temperature Reaction Baths: Used for low-temperature reactions, these are particularly suitable for the synthesis of temperature-sensitive chemical compounds, such as certain organic and pharmaceutical molecules.
Choosing and using these devices can significantly optimize reaction conditions, making experimental outcomes more controlled and stable.
3. Key Variables in Reaction Design
Optimizing reaction design requires careful consideration of multiple variables. Below are some key factors:
- Temperature: Reaction rates are highly dependent on temperature. Using equipment with precise temperature control (e.g., double glass reactors) allows researchers to test reactions at different temperatures and find optimal conditions.
- Pressure: Some reactions, such as hydrogenation, require high pressure. High-pressure stainless steel reactors can be used to optimize reactions in high-pressure environments, improving reaction rates and yields.
- Stirring Speed: Stirring improves the mixing of reactants, increasing reaction efficiency. By adjusting the stirring speed in reactors, researchers can optimize the mixing process, allowing for more uniform reactions.
- Solvent Choice: Different solvents can affect the solubility of reactants and reaction rates. Researchers can experiment with different solvent systems and optimize based on product yield and purity.
4. Practical Example of Reaction Optimization
Organic Synthesis Optimization Example
In a specific organic synthesis experiment, researchers used a double glass reactor to optimize the synthesis of an important intermediate. The reaction was carried out at a low temperature (-10°C), and the cooling medium in the double-layer reactor ensured stable conditions. By adjusting reaction time and stirring speed, they achieved the highest product yield while minimizing by-product formation.
In another example, researchers optimized a hydrogenation reaction using a high-pressure stainless steel reactor. By adjusting pressure and hydrogen flow rates at 200°C and 20 atm, they improved the product yield by 20%.
5. Data Collection and Reaction Monitoring
Real-time data collection and monitoring are crucial in the reaction optimization process. Using high-precision temperature and pressure sensors, researchers can track changes in reaction conditions, ensuring that each phase of the experiment operates under optimal conditions. Coupled with automated control systems, laboratories can implement automatic monitoring and adjustment, further enhancing experimental efficiency.
6. Conclusion
Reaction design and optimization are essential components of chemical laboratory research. By selecting the right laboratory equipment and optimizing reaction conditions, researchers can significantly increase yield, reduce by-product formation, and shorten experiment times. High-precision equipment, such as stainless steel reactors, double glass reactors, and low-temperature reaction baths, provides reliable technological support for reaction optimization. In the future, as instrumentation advances and automation becomes more widespread, chemical reaction design and optimization will become even more efficient and precise.