Introduction to Single Glass Reactor for Pharmaceutical Industry
In the pharmaceutical industry, achieving high-quality and reproducible results is essential for the development of safe and effective drugs. The single glass reactor for pharmaceutical industry plays a critical role in various stages of pharmaceutical production, from synthesis to formulation. This versatile equipment offers the precision required to conduct experiments under controlled conditions, ensuring that chemical reactions are consistent and yield high-quality products.
The single glass reactor for pharmaceutical industry is used in both research and large-scale production, making it an indispensable tool for pharmaceutical companies. This article will explore the key features, benefits, and applications of these reactors, as well as how they contribute to the efficiency and quality of pharmaceutical manufacturing processes.
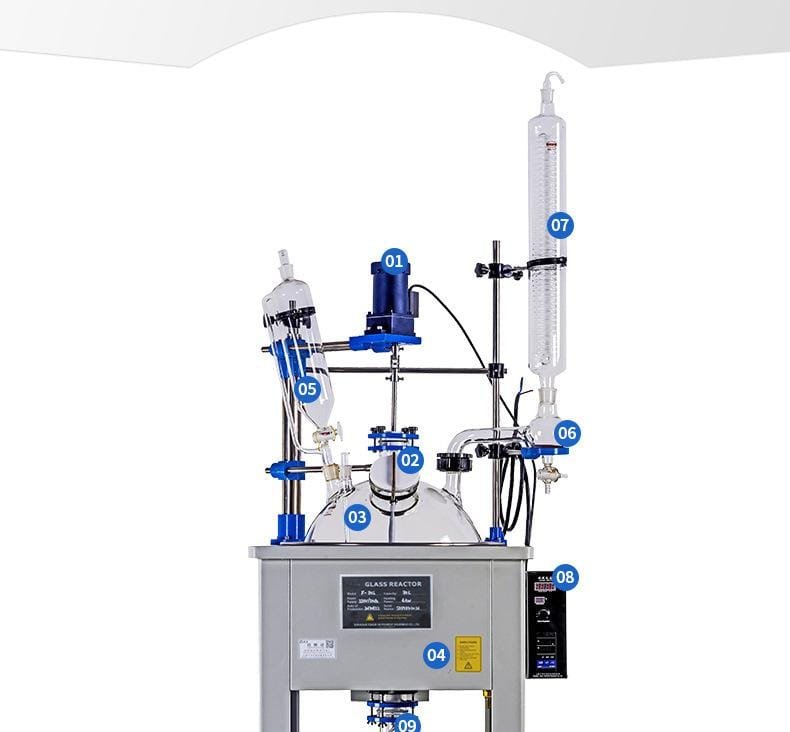
Key Features of Single Glass Reactor for Pharmaceutical Industry
When selecting a single glass reactor for pharmaceutical industry applications, it’s important to consider several key features that make these reactors suitable for use in the production of pharmaceuticals. These features include:
1. High-Quality Borosilicate Glass Construction
The material used in the construction of the reactor is one of the most critical factors. Single glass reactors for pharmaceutical applications are typically made from borosilicate glass, which is highly resistant to chemical corrosion, heat, and mechanical stress. This ensures the reactor can withstand the demanding conditions often required in pharmaceutical production without compromising safety or efficiency.
Borosilicate glass also provides transparency, which allows for real-time observation of reactions. This is particularly important when monitoring the progress of chemical processes such as drug synthesis or extraction.
2. Precise Temperature and Pressure Control
Temperature and pressure control are essential when working with sensitive pharmaceutical compounds. A single glass reactor for pharmaceutical industry comes equipped with advanced heating and cooling systems, ensuring precise regulation of temperature to maintain optimal reaction conditions. This is particularly critical for reactions that require careful temperature management to prevent decomposition or unwanted side reactions.
The ability to maintain stable pressure conditions is equally important, especially for reactions conducted under vacuum or at elevated pressures. Many reactors in the pharmaceutical industry are designed with built-in vacuum systems, making them suitable for a wide range of applications.
3. Efficient Mixing and Agitation
Efficient mixing is essential for ensuring uniform distribution of reactants and solvents in pharmaceutical reactions. Single glass reactors for pharmaceutical industry are equipped with robust stirring systems that ensure consistent agitation of the contents, even at higher viscosities. This feature is critical in processes such as emulsification, crystallization, and dissolution, where uniformity is key to achieving the desired product characteristics.
The stirrers in these reactors often come with adjustable speeds, allowing operators to tailor the mixing intensity according to the specific requirements of the reaction.
4. Modular Design for Flexibility
One of the standout features of a single glass reactor for pharmaceutical industry is its modular design, which allows for customization based on the specific needs of the reaction. For instance, reactors like the AKDF-50L Water Bath and Oil Bath Single Layer Glass Reactor offer both water and oil bath heating options, giving pharmaceutical manufacturers the flexibility to choose the best method for their specific processes. This adaptability is especially valuable in the pharmaceutical industry, where processes can vary significantly from one project to another.
Applications of Single Glass Reactor for Pharmaceutical Industry
The single glass reactor for pharmaceutical industry is used in various applications within pharmaceutical manufacturing, from research and development to full-scale production. Some of the most common uses include:
1. Chemical Synthesis
A single glass reactor for pharmaceutical industry is an essential tool for the chemical synthesis of active pharmaceutical ingredients (APIs). The ability to control temperature, pressure, and agitation makes it ideal for conducting reactions that are common in the synthesis of complex drug molecules. Researchers rely on these reactors to test different reaction pathways and optimize conditions to improve the yield and purity of the synthesized compounds.
2. Drug Formulation
In addition to chemical synthesis, single glass reactors are used in the formulation of pharmaceuticals. For example, when creating emulsions or suspensions for topical creams, ointments, or oral suspensions, reactors ensure the proper mixing of ingredients to achieve the desired texture and consistency. The precise control over mixing and temperature allows formulators to create high-quality pharmaceutical products that meet strict industry standards.
3. Extraction and Purification
Extraction processes, such as solvent extraction, are crucial in the pharmaceutical industry for isolating bioactive compounds from natural sources. The single glass reactor for pharmaceutical industry is used in these processes to ensure efficient extraction under controlled conditions. The reactor allows the extraction to occur at specific temperatures and pressures, which is essential for maximizing yield and purity.
After extraction, the reactor can also be used for the purification of compounds, ensuring that impurities are removed to obtain a high-quality product.
4. Research and Development
In pharmaceutical R&D, a single glass reactor for pharmaceutical industry is used to test new drug formulations, optimize chemical reactions, and study reaction kinetics. The ability to closely monitor reactions and adjust conditions in real-time makes these reactors a valuable tool in the development of new medications. Researchers can experiment with different parameters to fine-tune the reaction process and achieve the desired product characteristics.
Choosing the Right Single Glass Reactor for Pharmaceutical Industry
When selecting a single glass reactor for pharmaceutical industry applications, several factors should be taken into account:
1. Reactor Capacity
The size of the reactor will depend on the scale of production or research being conducted. For small-scale synthesis and R&D, reactors with capacities ranging from 1L to 5L may suffice. However, for larger-scale production or pilot testing, reactors with capacities up to 50L or more may be required.
2. Features and Customization
The reactor should come with features that are specifically designed for pharmaceutical applications, such as precise temperature control, vacuum systems, and robust agitation. Suppliers like EquilRxnLab offer customizable models that meet the unique needs of the pharmaceutical industry.
3. Safety Standards
Safety is critical when working with chemicals in the pharmaceutical industry. Ensure that the single glass reactor for pharmaceutical industry meets safety standards and includes built-in safety features such as pressure relief valves, secure seals, and temperature monitoring systems.
For more details on high-quality reactors designed for pharmaceutical applications, check out EquilRxnLab’s product catalog.
Where to Buy Single Glass Reactors for Pharmaceutical Industry
To ensure you’re getting the best value for your investment, purchase your single glass reactor for pharmaceutical industry from a reputable supplier. EquilRxnLab offers high-quality reactors with excellent customer support and a wide range of options to suit different pharmaceutical applications. Their AKDF-50L Water Bath and Oil Bath Single Layer Glass Reactor is a top choice for those looking for flexibility, reliability, and performance.