In-depth Analysis of Teflon-lined synthesis reactor in Modern Laboratories
Modern scientific research and industrial applications increasingly demand equipment that can withstand extreme conditions while ensuring precise and reliable outcomes. This article explores the capabilities and innovations surrounding the Teflon-lined synthesis reactor, a pivotal tool in high-pressure and high-temperature experimental setups. In our discussion, we examine its design intricacies, diverse applications, optimization strategies, and maintenance protocols, all framed within an academic and professional context. EquilRxnLab continues to lead with advanced engineering, ensuring that every product meets rigorous performance standards. To explore product details, visit the product page.
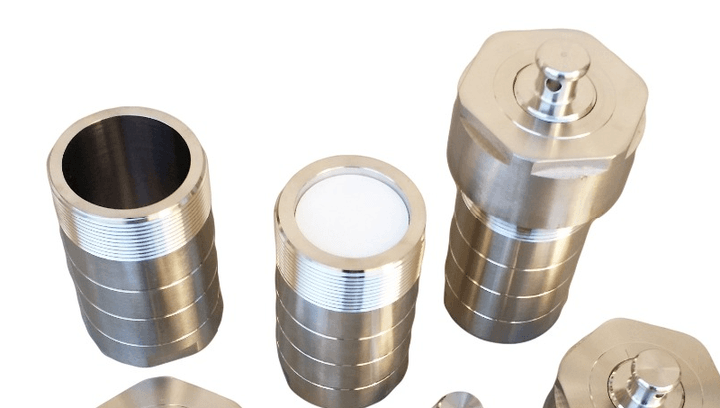
Design and Engineering of Teflon-lined synthesis reactor
The performance of a reactor in demanding laboratory conditions is primarily determined by its engineering and material composition. At the heart of the innovation lies the use of Teflon, a material known for its chemical inertness and exceptional resistance to corrosion. Engineers at EquilRxnLab have incorporated advanced manufacturing techniques to integrate Teflon linings seamlessly into reactor bodies, ensuring that the reactor maintains structural integrity under fluctuating pressure and temperature.
A critical design element is the uniform thickness of the Teflon lining, which prevents chemical interactions that could compromise reaction purity. Advanced computational modeling has been used to simulate thermal expansion and stress distribution, ensuring that the reactor performs optimally even during prolonged operations. This design not only minimizes maintenance intervals but also extends the lifespan of the equipment, which is crucial for continuous industrial and research applications.
Application Areas for Teflon-lined synthesis reactor
The versatility of this reactor spans across various fields, making it an invaluable asset in both academic and industrial laboratories. In material science, the reactor is employed for the synthesis of advanced nanomaterials where precise control over reaction conditions determines the quality of the final product. The inherent properties of Teflon minimize contamination risks, thereby enhancing the reproducibility of experiments.
In the pharmaceutical sector, researchers utilize the reactor for the synthesis of complex drug molecules, where purity and stability are paramount. Its robust design ensures that even the most reactive chemical species are safely contained, thus enabling the development of novel therapeutic agents. Environmental engineering also benefits from this technology, as the reactor facilitates studies on pollutant degradation and the synthesis of catalysts for wastewater treatment.
Additional applications include high-pressure crystallization experiments and the development of new polymers, where maintaining consistent reaction conditions is essential. For further information on related equipment, refer to the product catalog.
Optimization Strategies for Teflon-lined synthesis reactor
Achieving the best performance from such advanced laboratory equipment requires not only high-quality design but also the implementation of strategic operational protocols. Researchers and lab technicians are advised to calibrate temperature and pressure settings meticulously to match the specific requirements of their experiments. Optimizing these parameters is crucial to ensure that the reactor operates within its ideal performance envelope.
Implementing automation for parameter control can greatly improve reproducibility. Modern reactors are often equipped with digital controllers that allow real-time monitoring and adjustments, minimizing human error. Furthermore, integrating sensors that provide feedback on the internal state of the reactor can lead to dynamic adjustments during experimental runs, thus optimizing reaction conditions continuously.
Best practices in setup involve pre-conditioning the reactor to stabilize the Teflon lining, which may include a series of controlled thermal cycles. Such measures help in reducing initial variability and contribute to consistent performance. Researchers interested in innovative control systems can find additional technical resources and support by contacting EquilRxnLab through their contact page.
Maintenance and Safety in Teflon-lined synthesis reactor Operations
Operating under extreme conditions necessitates stringent maintenance routines to uphold both performance and safety standards. Regular inspection of the reactor’s Teflon lining is essential to detect any signs of wear or damage early. Non-abrasive cleaning agents should be used during maintenance to preserve the integrity of the lining and avoid introducing contaminants into sensitive reactions.
Safety protocols must be rigorously followed, especially when dealing with high-pressure systems. It is recommended that laboratory personnel undergo specialized training to handle such equipment, and that safety mechanisms—such as pressure relief valves—are routinely tested. Detailed standard operating procedures (SOPs) should be in place to manage potential hazards, ensuring that any incidents are minimized and that the reactor operates within safe parameters.
EquilRxnLab emphasizes the importance of a proactive maintenance schedule. Regular servicing not only prevents equipment failure but also contributes to enhanced safety during operations. For visual demonstrations and further safety tips, check out our YouTube channel and follow our updates on Instagram and Facebook.
Future Perspectives on Teflon-lined synthesis reactor Technology
The continuous evolution of chemical synthesis and material science drives the need for innovative reactor designs. Future advancements in the field are expected to focus on further enhancing the thermal and chemical stability of Teflon-lined systems. Researchers are exploring novel composite materials and hybrid designs that could potentially improve performance even under more rigorous conditions.
Integration with artificial intelligence and machine learning algorithms offers promising avenues for real-time process optimization. These technologies could enable reactors to autonomously adjust reaction parameters, thereby improving efficiency and reducing the likelihood of operational errors. Moreover, the trend toward miniaturization and modular reactor designs is anticipated to make high-performance synthesis more accessible to smaller research institutions and startups.
Collaboration between academic institutions and industry leaders such as EquilRxnLab is vital to drive these innovations. Future reactor designs may also incorporate sustainable practices, reducing energy consumption and improving overall environmental impact. With ongoing research and technological progress, the next generation of reactors will likely set new benchmarks for efficiency, safety, and versatility in laboratory environments.
In summary, the advanced engineering behind this reactor is a testament to the progress in modern synthesis technology. Through meticulous design, careful optimization, and rigorous maintenance protocols, the reactor sets a high standard for laboratory equipment. The integration of innovative control systems and safety measures ensures that researchers can push the boundaries of chemical synthesis while maintaining operational integrity. For those interested in exploring these advanced systems further, EquilRxnLab provides extensive resources and support. Discover more details by visiting the product page, and join our community on YouTube, Instagram, and Facebook. Continued engagement and research promise exciting developments in reactor technology, paving the way for groundbreaking discoveries in various fields of science and engineering.