Understanding the Role of Double-Layer Reactors in Industrial Processes
Double-layer reactors are essential tools for industrial processes, offering enhanced control over reaction conditions such as temperature and pressure. These reactors are designed to meet the rigorous demands of industries ranging from pharmaceuticals to energy production. In this article, we will explore the top features of double-layer reactors and how EquilRxnLab’s advanced reactor designs elevate industrial processes by providing precision, safety, and customization options.
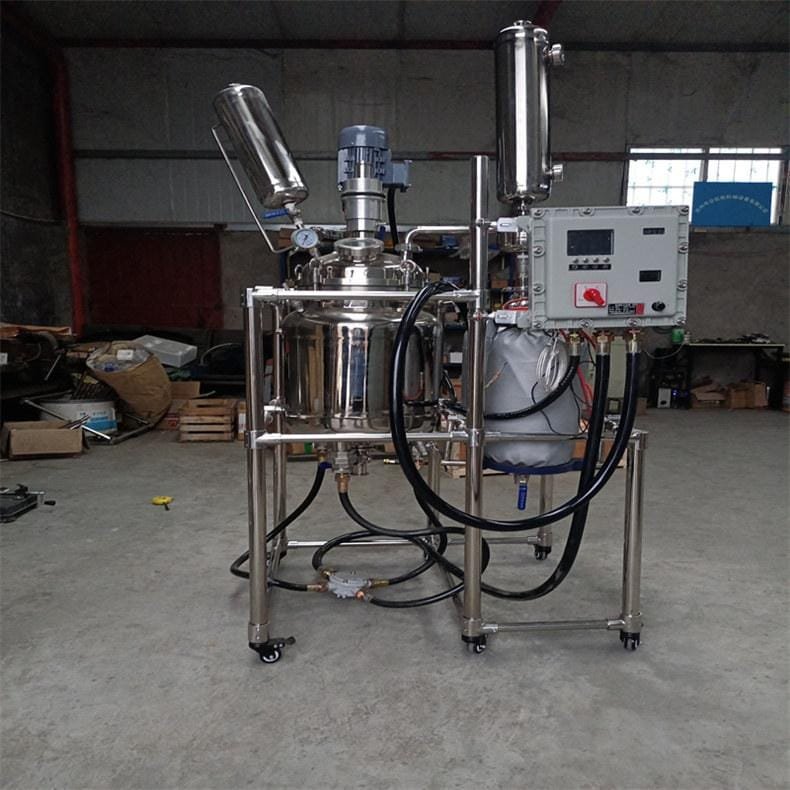
What is a Double-Layer Reactor?
A double-layer reactor is a type of chemical reactor that features an outer layer designed to control temperature and pressure during chemical reactions. The outer layer contains a jacket that can hold heating or cooling fluids, while the inner layer houses the reaction materials. This design allows for more precise temperature regulation, making double-layer reactors ideal for reactions that require strict thermal control.
Key Features of Double-Layer Reactors
Double-layer reactors are favored for their versatility and enhanced performance. Below, we’ll dive into the top features that make these reactors indispensable for various industrial applications:
1. Precise Temperature Control
The primary advantage of a double-layer reactor is its ability to maintain precise temperature control. By circulating heating or cooling fluids through the outer jacket, these reactors can easily maintain the desired reaction temperature. This is particularly important in industries such as pharmaceuticals and food processing, where small fluctuations in temperature can drastically affect product quality.
For instance, EquilRxnLab’s AKGF-100L Double-Layer Stainless Steel Reactor is designed to offer exceptional temperature control capabilities. Whether you need to heat or cool the reaction mixture, this reactor ensures optimal performance and uniformity.
2. Enhanced Safety Features
Safety is a major concern in any industrial setting, especially when dealing with high temperatures and pressures. Double-layer reactors, such as those provided by EquilRxnLab, are equipped with several safety features, including pressure relief valves, explosion-proof designs, and automatic shut-off mechanisms. These features minimize the risk of accidents and ensure safe operation, even in demanding environments.
With a focus on safety, EquilRxnLab’s reactors come with built-in protection mechanisms, allowing operators to work with confidence knowing that the equipment is designed to handle even the most challenging conditions.
3. High Pressure and Temperature Resistance
Double-layer reactors are capable of handling both high temperatures and pressures, making them suitable for a wide range of industrial processes. Whether you’re conducting high-pressure reactions or requiring elevated temperatures for synthesis, these reactors provide the necessary durability and performance.
The AKGF-100L Double-Layer Stainless Steel Reactor from EquilRxnLab is specifically designed to withstand extreme pressure and temperature conditions, ensuring that your reactions proceed smoothly without compromising on safety or efficiency.
4. Versatility in Applications
One of the standout features of double-layer reactors is their versatility. These reactors are used across multiple industries for various applications, including synthesis, crystallization, distillation, and fermentation. The ability to adjust temperature and pressure makes them ideal for processes that require precise conditions, such as in the pharmaceutical, food, and chemical industries.
EquilRxnLab’s reactors can be customized for specific applications, allowing users to fine-tune the reactor’s parameters to suit their exact needs. Whether you’re producing fine chemicals or conducting research and development, these reactors provide the flexibility required to optimize your processes.
5. Efficient Mixing and Stirring Systems
In many chemical processes, efficient mixing is crucial for achieving consistent results. Double-layer reactors are equipped with advanced mixing systems that ensure thorough blending of the reaction components. Whether you’re working with viscous materials or requiring high-intensity stirring, these reactors can be customized with a range of agitator designs to suit your application.
The AKGF-100L reactor comes with a highly efficient stirring system, providing excellent mixing and ensuring uniform reaction conditions throughout the process. The reactor’s mixing system can be adjusted to meet the demands of different types of reactions, improving overall efficiency.
6. Customizable Design
Every industrial process is unique, and the best reactors offer the flexibility to meet specific requirements. EquilRxnLab provides customizable options for their double-layer reactors, allowing clients to modify features such as the reactor size, jacket design, and mixing speed. This customization ensures that the reactor is perfectly suited to the client’s needs, whether for research, development, or full-scale production.
The AKGF-100L Double-Layer Stainless Steel Reactor is just one example of the customizable solutions offered by EquilRxnLab. With numerous customization options, you can tailor the reactor to fit your exact specifications.
7. Easy Maintenance and Cleaning
Maintaining a reactor can be a time-consuming task, especially when dealing with complex processes. Double-layer reactors, including those from EquilRxnLab, are designed with ease of maintenance in mind. The smooth, stainless steel surface ensures that the reactor is easy to clean and resistant to contamination. Additionally, the outer jacket can be accessed for routine inspections and maintenance, making it easier to keep the reactor in optimal condition.
For clients who require frequent cleaning, the EquilRxnLab reactors are an excellent choice, as they combine ease of maintenance with robust performance.
Industries That Benefit from Double-Layer Reactors
Double-layer reactors are used in various industries where precise control over temperature and pressure is required. Here are some key industries that rely on these reactors:
1. Pharmaceutical Industry
Double-layer reactors are extensively used in the pharmaceutical industry for the synthesis of active pharmaceutical ingredients (APIs). The ability to control temperature and pressure is critical to ensuring the purity and consistency of pharmaceutical products.
2. Chemical Manufacturing
Chemical manufacturers use double-layer reactors for a variety of processes, including polymerization, crystallization, and reaction kinetics studies. The versatility of double-layer reactors makes them an essential tool in the chemical industry.
3. Food and Beverage Industry
The food and beverage industry requires reactors for processes such as fermentation, emulsification, and concentration. Double-layer reactors provide the necessary control to achieve consistent product quality and flavor profiles.
4. Energy and Biofuel Production
In biofuel production, double-layer reactors are used for transesterification processes, where oils are converted into biodiesel. The reactor’s ability to withstand high temperatures and pressures is vital to this process.
Why Choose EquilRxnLab’s Double-Layer Reactors?
EquilRxnLab stands out for its innovative reactor technology, which is designed to enhance industrial processes. With a focus on performance, safety, and customization, EquilRxnLab reactors provide the perfect solution for industries that demand precision and reliability.
For more information about EquilRxnLab’s reactors, visit the product page for the AKGF-100L Double-Layer Stainless Steel Reactor.
Explore More from EquilRxnLab
To learn more about the range of reactors available, check out EquilRxnLab’s product catalog. Stay updated with the latest innovations in reactor technology by visiting EquilRxnLab’s YouTube channel, Instagram, and Facebook.
Double-layer reactors are indispensable for industries that demand precise control over reaction conditions. EquilRxnLab offers high-performance, customizable reactor solutions that are built to enhance efficiency, safety, and reliability across a wide range of applications.